Case Study: Upgrading an old Makeup Air Unit to a Heat Pump
Transforming Fresh Air Delivery with Modern Heat Pump Technology
Project Overview: A 20-story residential high-rise in Atlanta underwent an ASHRAE Level II Energy and Water Assessment conducted by Verdius Energy. As part of the assessment, the existing makeup air unit was identified for replacement with a more efficient heat pump system. This measure was highlighted due to its significant potential for energy savings and operational efficiency improvements.
Existing System:
- Make: Aaon
- Model: RM-025-8-0
- Year Installed: 2005
- Cooling capacity: 25 Tons
- Efficiency: 14.2 SEER
- Heating capacity: 75 kW
- COP: 1
- Supply fan: 3 HP
- Outside airflow: 4,500 CFM
Identified Issues:
- Although the existing unit provided necessary ventilation, it is energy-intensive due to its reliance on electric resistance heating.
- Over time, the unit's components, despite replacements and maintenance, have aged and operate less efficiently compared to modern HVAC technology.
Considerations:
- The building exhaust is local and distributed throughout the building, so a heat recovery system using an enthalpy wheel could not be used.
- The location of the unit on the roof meant it could only be replaced via airlift. Since the unit would need replacement anyway, the marginal cost of installing a heat pump was considered, instead of the fully burdened cost.
Proposed Solution:
- Replacement with a modulating heat pump makeup air unit of similar size and capacity.
- Increased cooling efficiency, from 14.2 SEER to 22.5 SEER, a 50% increase.
- Increased heating efficiency, from 3.1 HSPF to 10.1 HSPF, a 3X increase due to the use of heat pump technology.
- Benefits:
- Energy Efficiency: Heat pump technology offers higher efficiency by transferring heat from outside, instead of generating it through electric resistance.
- Operational Savings: Reduced electrical consumption for heating and cooling, leading to lower utility bills.
- Environmental Impact: Proper disposal of ozone-depleting R-22 refrigerant and decreased greenhouse gas emissions due to improved efficiency.
Savings and Performance Metrics:
- Electricity savings: 105,000 kWh/year
- Annual cost savings: $9,800
- Project cost: $15,600 (marginal cost of heat pump over baseline)
- Simple payback period (SPP): 1.6 years
Incentives and Rebates:
Pending rebate through Georgia Power Custom Projects and Building Tune-Up programs, estimated at $5,000, reducing the net project cost to $4,800.
Additionally, the project qualified for a $20,000 Section 179D deduction.
Implementation Plan:
- Solicitation: Prepared a design-build RFP and engaged qualified HVAC contractors with experience in high-rises and airlifts.
- Timeline: To minimize disruption, the replacement was scheduled during the shoulder season.
- Verification: Post-installation commissioning and measurement & verification (M&V) to ensure the unit operates as expected and achieves the projected savings.
Conclusion: Upgrading the makeup air unit to a heat pump instead of a code-minimum replacement represents a strategic investment in energy efficiency. The significant cost savings, combined with a short payback period and environmental benefits, made this measure a high-priority recommendation from the energy assessment. This project not only aligns with the property's sustainability goals but also enhances the building's operational performance and residents' comfort.
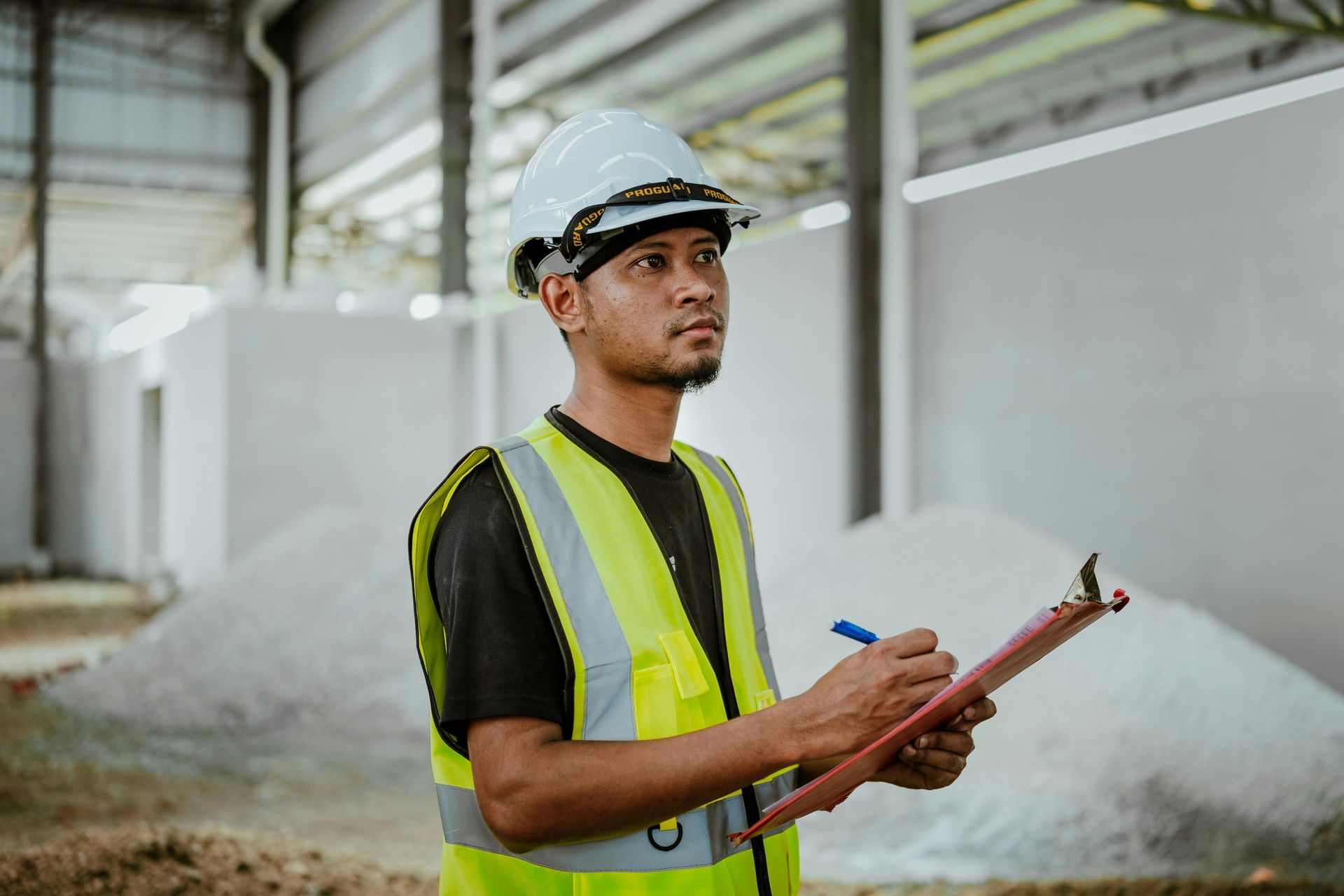