Merits of Adding Attic Insulation in a 1990's Condo Unit
Insulation is the opposite of sexy, but taking a good look at it may pay off
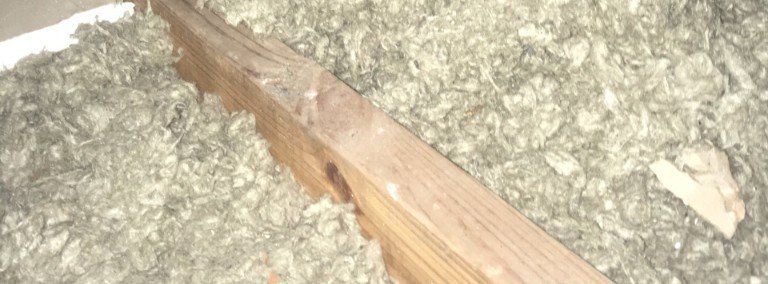
Recently I had the pleasure of working with a young couple who own a single story condo unit in the clear lake area of Houston Texas. They reached out for a free remote energy audit and mentioned that they use a lot more electricity than when they lived in Florida in a similar style condo unit. The home is about 1,000 square feet, and built in the 1990s. A primary complaint they brought up was that the house would get uncomfortably hot, the air conditioning would cycle on, and the house would be cooled and repeat. This would occur at a reasonable setpoint of 76 degrees. Immediately, I realized the homes air conditioning was oversized. It is a 2.5 ton split system air conditioner that is original to construction. Obviously, the 25 year old unit should be replaced with a right-sized as soon as possible, but the couple insisted to wait until it failed and that lower cost measures be taken in the meantime.
The condo unit had attic access and I took at a look at the insulation in the attic. Not to my surprise there appeared to be minimal insulation. The attic insulation was blown-in cellulose fiber, about two to 2 ½ inches deep which is way below R-30 code-mandated thickness. Either the construction company skimped on the insulation (not uncommon in multi-family construction) or we had some serious settling occur over the past 25 years. I believe it was a bit of both. Adding insulation to this attic space was going to be an important part of this customer’s solution package. It also occurred to me that the air conditioning may have actually been sized properly given how little insulation there was!
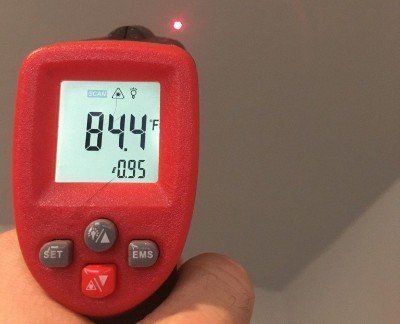
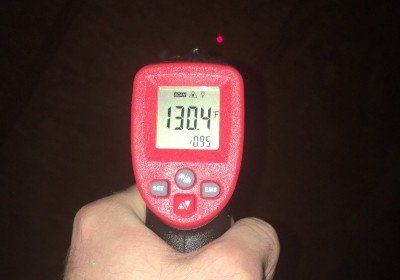
Below I will present the calculations needed to justify installing additional attic insulation. The home has 1,080 square feet of attic area. A significant chunk of that area is the vaulted ceiling in the living room, which has fiberglass batts insulating the vaulted area and the knee-walls. A few lengths of the batt insulation on the knee walls were falling off, so there is only drywall insulating the 130 degree attic - which is typical for a hot sunny day - from the conditioned space below. As stated earlier, there is about 2 inches of insulation. Some areas have 4 inches, some have none, but on average, let’s go with two inches. Below is a chart detailing the attic surfaces:
From this data we can determine the R-value of the entire attic space -- 243 BTU/°F·h. Since hot moves to cold, if our attic is 130 degrees and our space is 76 degrees, the space is gaining heat through the attic at a rate of 13,000 BTUs per hour, which is a little over one ton of cooling. That’s right, about 40% of our cooling during a hot day is used just to offset the heat gain from the attic.
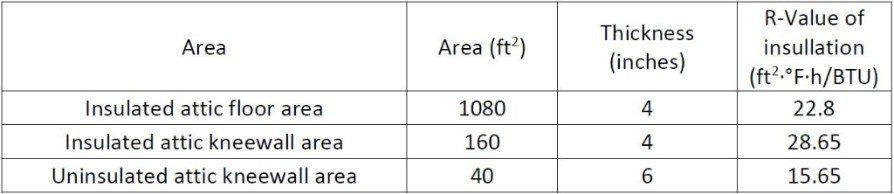
Now, let’s add 4 inches of blown-in cellulose insulation to the insulated areas, and 6 inches to the uninsulated attic knee wall area. We get an attic space R-Value of 56 BTU/°F·h. We have reduced our heat transfer through the attic to 3,000 BTUs per hour, a reduction of nearly 80%.
That’s great, but what about when it’s not a hot sunny day in June? We need to figure out the total heat transfer throughout the year and then we can determine how many BTUs are moving down through the attic.
For this, we are going to use cooling and heating degree days. Degree days are a measure of ambient temperature difference from a set balance point, usually 65 degrees, summed over the course of a year. If for example, the average daily temperature of today, May 7th is 82 degrees, and the balance point is 65 degrees, we have 17 cooling degree days today. The total annual degree days would be the sum of this calculation over the course of a year. Houston has an average of 3,719 cooling degree days and 876 heating degree days according to the Houston Hobby airport weather station. We can use these numbers for our calculation, however, we need to take into account that the attic is usually a bit hotter than the ambient temperature. In order to do that, I will change the balance point from 65 to 55 degrees, which assumes the attic is, on average 10 degrees hotter than the outdoors on heating degree days. With our new balance point, we have 6746 cooling degree days, which almost doubles our total cooling degree days. A ten degree difference in the attic really changes things. In order to determine the total heat gain through the attic over the course of a year, we must find multiply our 243 BTU/°F·h by 6746 °F·days/year and 24 h/day.
Holy Moses, that’s a big number. Let’s get that in to something more understandable. 12,000 BTUs per hour is one ton heat transfer. That means we have 3,279 ton-hours of heat transfer through the attic over the course of a year, which equates to 3,279 ton-hours of air conditioning use over the course of a year. Dividing this buy 2.5 tons, the size of our air conditioner, we find that the air conditioner is running 1,311 hours per year just to remove the heat gain coming through the attic.
I’ve performed the same calculation of heat transfer with the new addition of insulation. The air conditioning use is reduced to 756 ton-hours. We can convert this number into actual kWh consumed per year using the SEER rating of the air conditioner. The unit is rated at SEER 10, but due to age, I am assuming it is a SEER 9 at this point. Given this information, 4,371 kWh per year are consumed cooling the heat coming through the attic as it is. With new insulation installed, we reduce this to 1,007 kWh, a 3,364 kWh reduction. At 10 cents per kWh, this equates to a $336 annual savings in energy cost.
But how much will this cost? That is an important factor that the client weighed in this case. The answer made the choice even more clear. 433 cubic feet of cellulose insulation are needed to achieve the insulation levels used in the calculations above. 25 cubic foot bundles of cellulose go for about $10 a bundle and 18 bundles are needed. Actual insulation material cost should came in right above $180 dollars, air sealing, labor and overhead costs are expected to be $500. The total all-in cost to the customer was $680 dollars, meaning this project will pay back in two years.
I will post a follow up once the project is completed and we should see some promising results in the coming months.In the meantime, check back weekly for new blog posts!
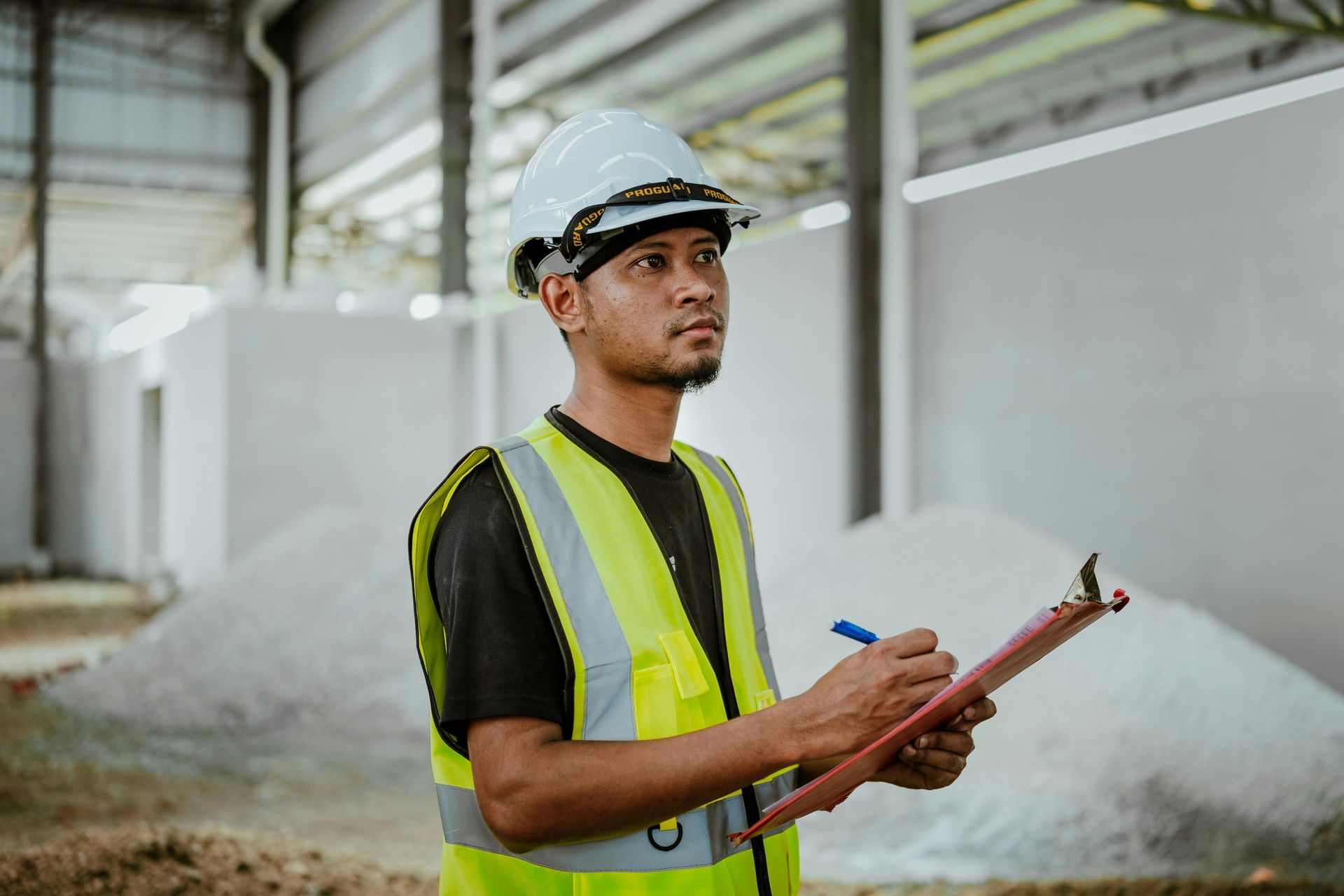